Understanding the Role of a Plastic Injection Mold Manufacturer
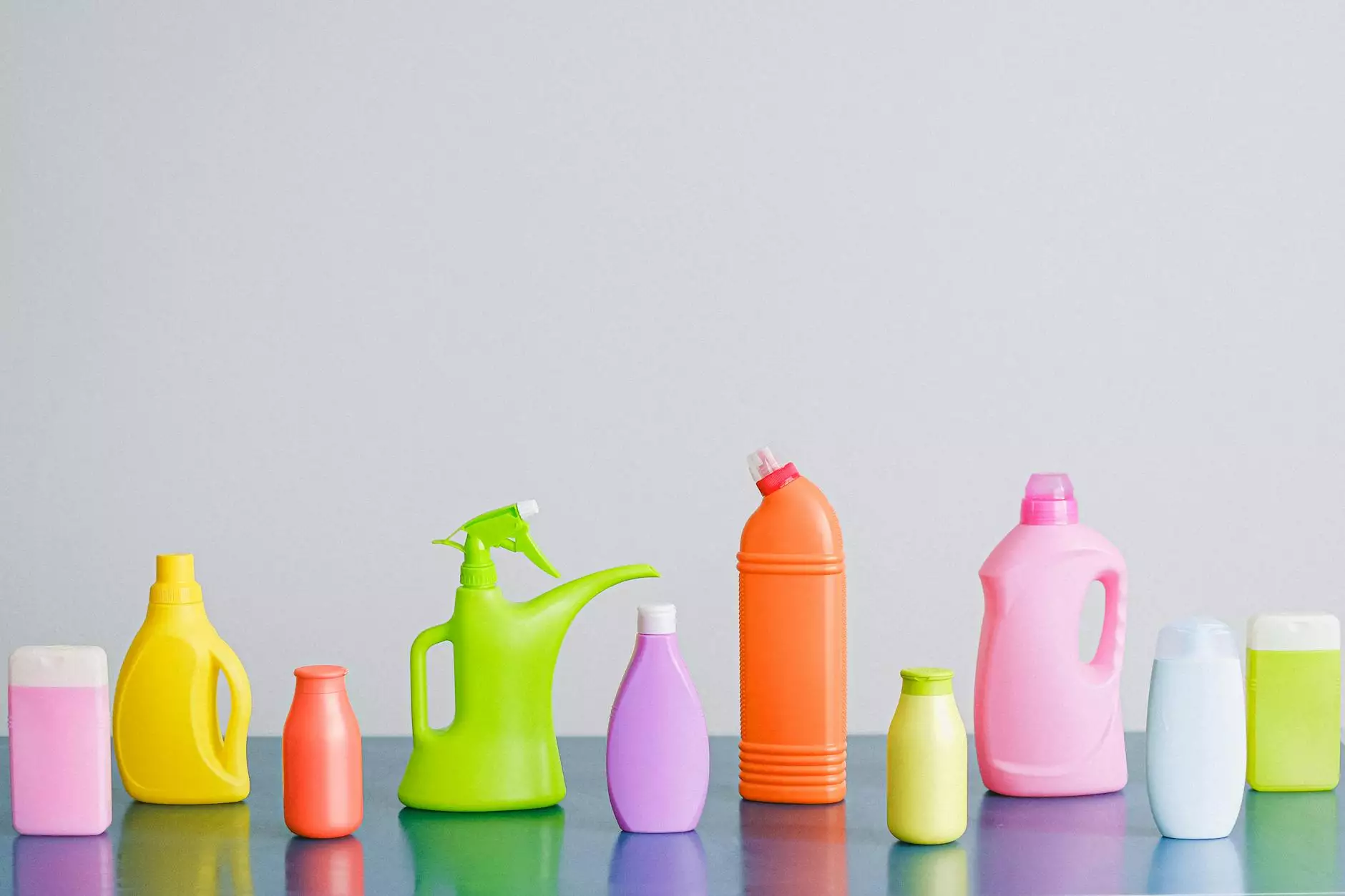
In today’s competitive manufacturing landscape, understanding the intricate details regarding a plastic injection mold manufacturer is vital for any business involved in the production of plastic parts. The role that these manufacturers play is fundamental, not only to the efficiency of the production process but also to the cost-effectiveness and quality of the final products.
What is Plastic Injection Molding?
Plastic injection molding is a manufacturing process that involves creating parts by injecting molten plastic into a pre-designed mold. This technique is revered for its ability to produce high volumes of identical parts with exceptional detail and precision. Understanding this process is key to appreciating the importance of choosing the right mold manufacturer.
Key Benefits of Plastic Injection Molding
- Cost Efficiency: Once the initial mold is created, producing each part becomes relatively inexpensive.
- High Precision: Capable of creating complex shapes with tight tolerances.
- Material Variety: Compatible with a wide range of materials, including thermoplastics and thermosetting polymers.
- Scalability: Ideal for both small and large production runs.
Choosing the Right Plastic Injection Mold Manufacturer
Choosing a reputable plastic injection mold manufacturer can be an overwhelming task due to the multitude of options available. However, focusing on several critical factors can guide you towards making an informed decision:
1. Experience and Reputation
Experience is the backbone of any successful manufacturing operation. A manufacturer with years of experience not only possesses technical skills but also a profound understanding of manufacturing challenges. Research potential manufacturers carefully:
- Look for customer reviews and testimonials.
- Examine their portfolio of previous work.
- Inquire about their years in business and expertise in specific sectors.
2. Technical Capabilities
Not all manufacturers are equipped to handle the same projects. Assessing their technical capabilities is essential:
- What types of molds can they produce?
- Do they specialize in multi-cavity molds or family molds?
- Are they able to incorporate advanced technologies such as hot runner systems?
3. Quality Assurance Processes
The quality of the molds produced will directly affect the quality of your finished products. It's crucial that potential manufacturers have robust quality assurance processes in place:
- What certifications do they hold (e.g., ISO 9001)?
- What quality control measures do they implement throughout the production process?
- Are they willing to provide samples for testing?
4. Lead Time and Flexibility
The lead time for mold production can greatly influence your project timelines. Ensure that the plastic injection mold manufacturer you choose can meet your deadlines without compromising quality:
- Ask for detailed timelines for mold creation and product delivery.
- Inquire about their ability to adapt to changes in order quantities or specifications.
5. After-Sales Support
Post-production support is often overlooked but is crucial to a successful partnership. Good manufacturers will offer:
- Maintenance services for molds.
- Technical support for troubleshooting issues.
- Open lines of communication for feedback and improvement.
The Importance of Material Selection
Choosing a reputable plastic injection mold manufacturer also includes understanding the materials used in production. Polymer materials are diverse, with each type offering unique properties:
Common Materials Used in Plastic Injection Molding
- ABS (Acrylonitrile Butadiene Styrene): Known for its toughness and impact resistance.
- Polycarbonate: Highly durable and transparent plastic, ideal for optical applications.
- PP (Polypropylene): Often used for packaging and automotive components due to its lightweight and chemical resistance.
- POM (Polyoxymethylene): Offers excellent mechanical properties and is resistant to wear and fatigue.
Cost Considerations When Working with Plastic Injection Mold Manufacturers
Cost is a significant consideration when choosing a plastic injection mold manufacturer. Factors influencing cost include:
- The complexity of the mold design.
- The type of material selected for the mold and the final product.
- The quantity of parts required (higher quantities usually lower the price per unit).
- Geographical location and shipping fees for manufacturers.
It’s important to remember that the cheapest option isn’t always the best. Balance cost with quality and service to find a supplier that meets your needs.
Case Studies: Success Stories in Plastic Injection Molding
Understanding how other businesses have succeeded with their plastic injection mold manufacturer can provide insights for your own operations. Here are two notable case studies:
Case Study 1: Automotive Component Production
A leading automotive company partnered with a specialized plastic injection mold manufacturer to produce a series of components for electric vehicles. By utilizing both their robotics capabilities and advanced molding technologies, the manufacturer was able to:
- Reduce lead times by 30%.
- Lower production costs by utilizing recycled materials.
- Improve product performance through innovative design features.
Case Study 2: Consumer Goods Packaging
A consumer goods company improved its packaging line by working with an experienced plastic injection mold manufacturer. The outcomes included:
- Enhanced package durability, leading to reduced damage in transit.
- Increased machine efficiency by 20% due to expertly crafted molds.
- Timely updates to product designs with a focus on sustainability.
Future Trends in Plastic Injection Molding
As technology continues to evolve, the world of plastic injection molding is not exempt from change. Here are some trends to keep an eye on as you consider your next project:
1. Smart Manufacturing
The integration of smart technologies such as AI and IoT is revolutionizing the manufacturing process. These technologies enable:
- Real-time monitoring of production processes.
- Predictive maintenance, reducing machine downtime.
- Data analysis for optimizing production efficiency.
2. Sustainable Practices
With an increasing focus on sustainability, many manufacturers are turning to eco-friendly practices, including:
- Using bioplastics and recyclable materials in production.
- Implementing energy-efficient machinery.
- Practicing waste reduction techniques throughout the manufacturing process.
3. Rapid Prototyping
The demand for rapid prototyping is growing, allowing companies to quickly test product designs before full-scale manufacturing. Advanced techniques like 3D printing are becoming increasingly common in this area.
Conclusion: Making the Right Choice
In conclusion, selecting the right plastic injection mold manufacturer is a decision that can significantly impact your business’s success. By considering factors such as experience, quality, technical capabilities, and future trends, you can make an informed choice that aligns with your operational goals. DeepMould, with its extensive expertise in metal fabrication and plastic injection molding, stands ready to meet your manufacturing needs while ensuring excellence in quality and service.
To learn more about how we can help you achieve your production goals, visit our website at deepmould.net.