The Comprehensive Guide to Pressure Die Casting Products
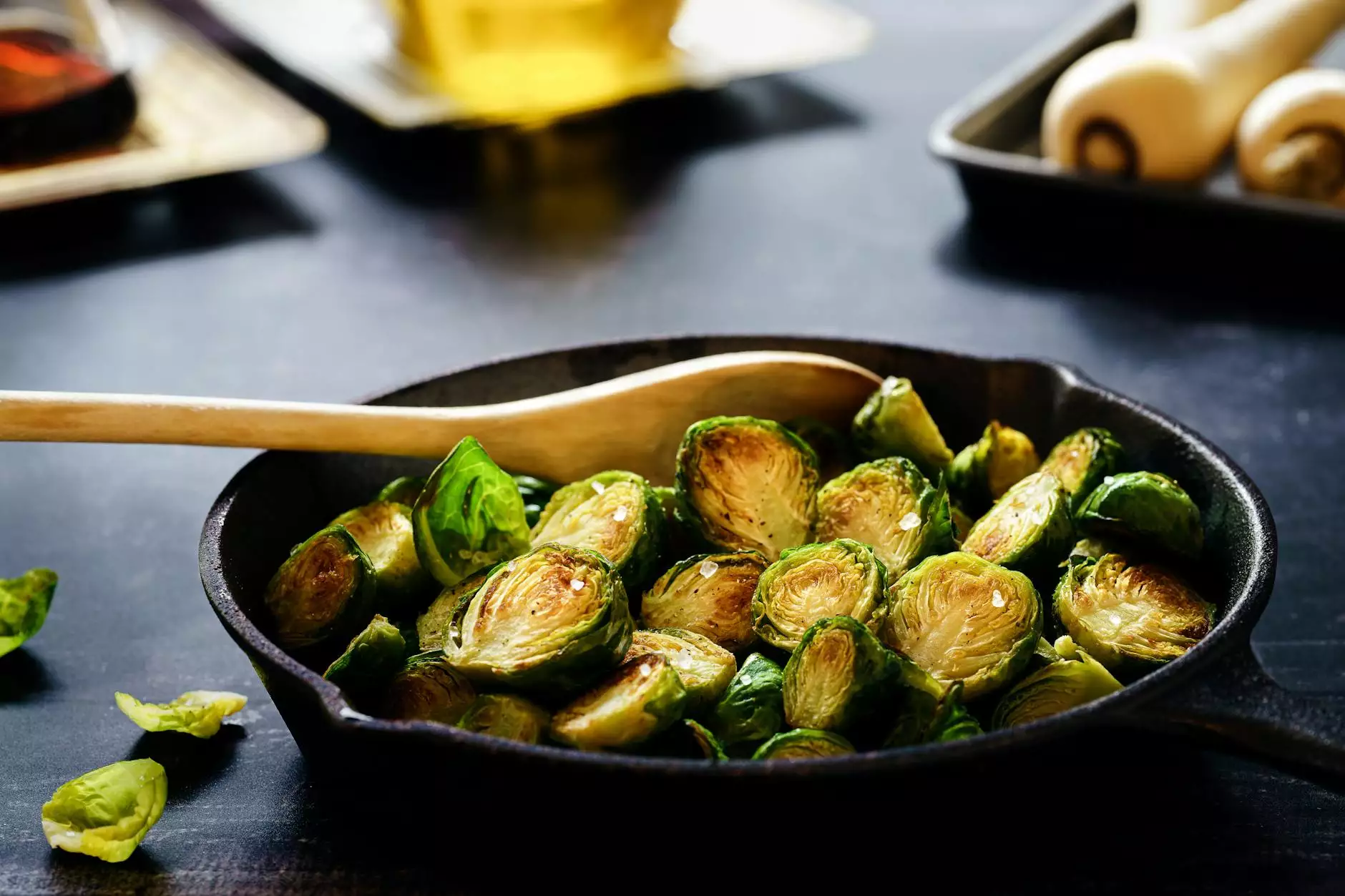
In today's competitive manufacturing landscape, pressure die casting products play a vital role in producing high-quality components with precision and efficiency. This article delves into the intricacies of pressure die casting, its advantages, the processes involved, and its diverse applications in various industries.
Understanding Pressure Die Casting
Pressure die casting is a highly productive method of creating metal parts from non-ferrous metals, primarily aluminum, zinc, and magnesium. This technique involves forcing molten metal under high pressure into a mold cavity. The pressure helps to fill the mold quickly and ensures that even the finest details are captured perfectly.
The Process of Pressure Die Casting
The process of pressure die casting can be broken down into several key steps:
- Melt Preparation: The manufacturing process begins with the melting of the metal alloy at high temperatures. This phase is crucial as it determines the quality of the final product.
- Injection: Once the metal is molten, it's injected into the mold using a hydraulic mechanism. The pressure applied can reach up to 2000 psi.
- Cooling: After the mold is filled, the metal is allowed to cool and solidify. This phase can take just seconds to a couple of minutes, depending on the thickness of the part.
- Mold Opening: Once cooled, the mold opens, and the cast part is ejected. At this stage, minor finishing processes may be initiated.
- Trimming and Finishing: Any excess material from the casting process, known as flash, is trimmed away. Further finishing processes like polishing, coating, or painting may follow.
Advantages of Pressure Die Casting Products
The popularity of pressure die casting products can be attributed to their numerous advantages:
- High Precision: The method produces parts with excellent dimensional accuracy, which is essential for tight tolerances in various applications.
- Robustness: Components created using die casting are stronger and more resilient compared to those made through other methods like sand casting.
- Surface Finish: The die-casting process provides an excellent surface finish with minimal need for post-processing, reducing manufacturing time and costs.
- Complex Geometries: The process allows for the creation of complex shapes that would be difficult or impossible to achieve with other manufacturing techniques.
- Cost Efficiency: Although the initial setup costs are high due to the need for a custom mold, the longevity and repeatability of the process lead to lower per-unit costs for large production runs.
Applications of Pressure Die Casting Products
Due to its versatility, pressure die casting finds applications across various industries, including:
Automotive Industry
The automotive sector is one of the largest consumers of pressure die casting products. Components like engine blocks, transmission cases, and other complex parts benefit from the precision and strength of die casting.
Aerospace Industry
In the aerospace industry, where weight and strength are crucial, die-cast components are extensively used in aircraft engines and structures. The ability to produce lightweight yet durable parts is a game changer in this field.
Medical Equipment
Medical devices require a high level of precision and reliability. Pressure die casting products are frequently used in the manufacturing of surgical instruments and components of medical devices, ensuring they meet stringent industry standards.
Consumer Electronics
From casings for smartphones to parts of home appliances, the consumer electronics sector relies on pressure die casting for high-quality components that meet aesthetic and functional requirements.
Choosing the Right Metal Fabricator for Your Pressure Die Casting Needs
Selecting the right supplier for pressure die casting products is critical for ensuring quality and efficiency in your manufacturing process. Here are some key factors to consider:
Experience and Expertise
Look for manufacturers with a proven track record in die casting. Their experience in handling complex designs and troubleshooting will save you time and money.
Technology and Equipment
Assess whether the fabricator uses advanced technology and up-to-date equipment. State-of-the-art machines can produce better quality components with faster turnaround times.
Quality Control Processes
Robust quality control measures are essential. Ensure the manufacturer adheres to strict quality standards and can provide material certifications and testing reports.
Customization Capabilities
A good metal fabricator should be able to cater to your specific requirements, including custom designs and unique specifications.
Customer Support
Reliable customer service is crucial for addressing any concerns or adjustments needed during the production process. Choose a supplier that is responsive and supportive.
The Future of Pressure Die Casting
The future of pressure die casting products looks promising, driven by ongoing advancements in materials and processes. Below are some anticipated trends:
Increased Automation
With the rise of Industry 4.0, automation in pressure die casting will enhance production efficiency, minimize human error, and decrease labor costs.
Eco-Friendly Practices
As sustainability becomes a priority, manufacturers are integrating eco-friendly practices in their operations, which includes recycling scrap metal and reducing energy consumption during the production process.
3D Printing Integration
The integration of 3D printing technologies with die casting could allow for rapid prototyping, creating molds faster and with less expense.
Material Innovations
New alloys and hybrid materials are being developed to meet increasing performance demands, enabling manufacturers to create even stronger and more lightweight components.
The Role of DeepMould in Pressure Die Casting
As a leading entity in the metal fabricators niche, DeepMould excels in the production of high-quality pressure die casting products. With state-of-the-art facilities and a dedicated team of professionals, DeepMould offers:
- Tailored Solutions: Custom designs to fulfill specific client needs.
- Precision Engineering: Utilizing advanced die casting technology for accurate results.
- Comprehensive Support: From design consultation to after-sales service, we ensure a seamless customer experience.
In conclusion, pressure die casting is a sophisticated manufacturing process that serves a myriad of industries by producing high-quality products efficiently and accurately. Understanding its benefits, applications, and the future potential is vital for businesses looking to leverage this innovative technology.
For more information about pressure die casting products and how they can benefit your business, visit deepmould.net.