Understanding the Role of Precision Injection Mould Suppliers in Metal Fabrication
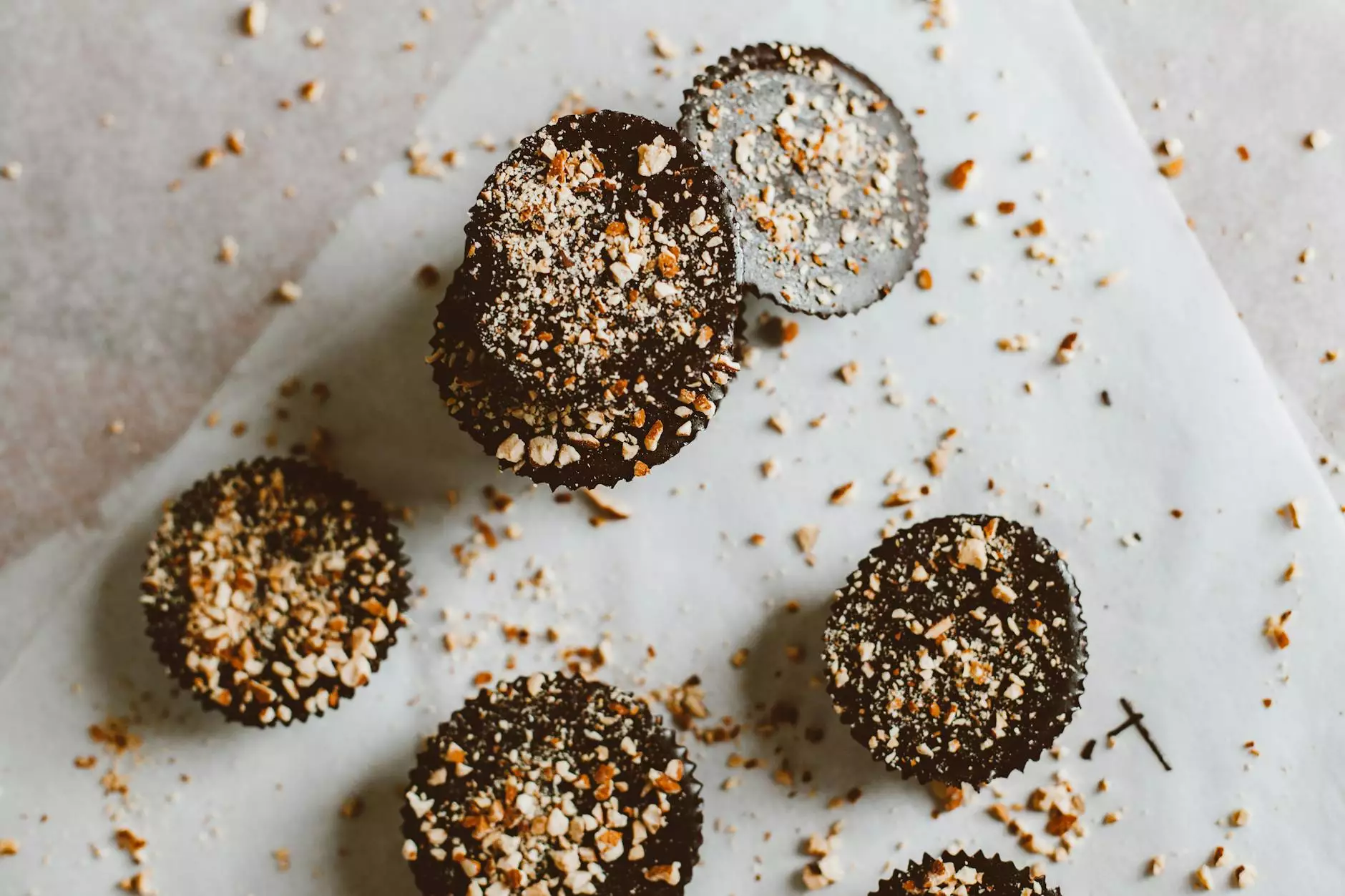
In the world of manufacturing, the significance of precision injection mould suppliers cannot be overstated. As industries seek to enhance productivity and ensure consistency in product quality, the reliance on specialized suppliers has increased. This detailed article delves into the importance of precision injection mould suppliers, their contributions to metal fabrication, and how they pave the way for innovation and efficiency in manufacturing processes.
What are Precision Injection Moulds?
Precision injection moulds are intricate tools used to create metal parts with a high degree of accuracy. They are essential in various manufacturing sectors where precision and quality are paramount. These moulds allow manufacturers to produce complex shapes that would be difficult or impossible to achieve through traditional machining methods.
Key Components of Precision Injection Moulds
- Mould Base: This is the foundational part of the injection mould, providing the necessary support for other components.
- Cavity and Core: The cavity is where the material is injected, while the core shapes the inside of the part.
- Cooling Channels: These are integrated into the mould to control temperature during the injection process and enhance cycle times.
- Ejector System: This system removes the finished part from the mould once it has cooled and solidified.
The Importance of Precision in Manufacturing
Precision is critical in manufacturing as it directly impacts product quality, performance, and reliability. Here’s why precision matters:
1. Enhanced Product Quality
When components are manufactured with high precision, the likelihood of defects decreases significantly. This leads to higher customer satisfaction and reduced waste.
2. Cost-effectiveness
While the initial investment in precision equipment can be high, the long-term savings are substantial. Lowering the rate of defective parts reduces costs associated with rework and scrap.
3. Improved Efficiency
Precision injection moulding allows for quicker production cycles, ensuring that manufacturers can meet demand without sacrificing quality.
The Role of Precision Injection Mould Suppliers
Precision injection mould suppliers are integral to the success of manufacturing processes. They provide not only the moulds but also expertise and support throughout the production life cycle.
Providing Expertise and Innovation
These suppliers often invest heavily in research and development to innovate and improve injection moulding technologies. This includes:
- Advanced Materials: Using the latest materials to enhance the durability and efficiency of moulds.
- Technological Integration: Incorporating advanced technologies, such as CAD/CAM tools, for design and production.
- Customization: Offering tailored solutions that meet specific client needs and industry demands.
Quality Assurance Practices
One of the key advantages of working with reputable precision injection mould suppliers is their commitment to quality assurance. Rigorous testing and quality control checks ensure that every mould meets the highest standards before shipment.
Choosing the Right Precision Injection Mould Supplier
Selecting a supplier for precision injection moulds is crucial. Here are some considerations to keep in mind:
1. Industry Experience
Choose suppliers with a proven track record in your specific industry. Experience brings a wealth of knowledge regarding specific requirements and challenges.
2. Technological Capabilities
Look for suppliers that utilize cutting-edge manufacturing technologies and continuously invest in process improvements. This not only ensures that you receive high-quality products but also that their methods are efficient and modern.
3. Customer Support
Strong customer support can make a significant difference in the manufacturing process. Supplier responsiveness and willingness to engage in problem-solving contribute greatly to a successful partnership.
Trends in Precision Injection Moulding
As industries evolve, so do the technologies and practices surrounding precision injection moulding. Here are some notable trends:
1. Sustainability Initiatives
Many manufacturers now seek suppliers who prioritize sustainability. This includes the use of eco-friendly materials and processes that reduce waste and energy consumption.
2. Automation and Smart Manufacturing
The integration of automation in injection moulding processes is on the rise. This trend not only speeds up production but also enhances precision and minimizes human error.
3. Advanced Quality Control Techniques
Utilizing advanced inspection technologies such as AI-based machine vision systems allows suppliers to guarantee that products meet exact specifications consistently.
Conclusion: The Future of Precision Injection Mould Suppliers
The role of precision injection mould suppliers in the manufacturing landscape is becoming increasingly significant. As industries demand higher quality, enhanced efficiency, and innovative solutions, these suppliers will be at the forefront of delivering results that meet and exceed expectations. Thus, establishing a robust relationship with a leading precision injection mould supplier, such as those represented by Deep Mould, is indispensable for businesses aiming to thrive in today's competitive market.
By emphasizing precision, quality, and continuous improvement, businesses can ensure they remain relevant and successful, not just in the metal fabrication sector, but across the board.